Investigation of static and dynamic properties of MIM β titanium alloys
November 21, 2022
Metastable β titanium alloys offer a combination of excellent biocompatibility and mechanical properties, particularly toughness and fatigue, and, as such, find extensive applications in both the lightweight structural and biomedical fields. In addition, β titanium alloys can be engineered to allow for tuning the chemical composition of non-toxic alloying elements in such a way that low Young’s modulus, as well as good biocompatibility, can be achieved. However, β titanium alloys produced by binder-based powder technologies, such as Metal Injection Moulding, can generally have more processing-related defects than those of the more common α/β type Ti-6Al-4V alloys made by non-binder powder metallurgy processes. These defects in as-sintered β Ti-parts include: residual porosity, high impurity levels, and coarse-grained microstructures.
A joint research project undertaken by Northwest Institute for Non-ferrous Metal Research, Xi’an, China, and the Helmholtz-Zentrum Hereon, Geesthacht, Germany, set out to study, in the light of existing literature, the influence of the above mentioned defects on the damage tolerances of MIM β titanium alloys under static and dynamic loading. The results of this research have been published in a paper by the authors Peng Xu, et al, in Powder Metallurgy journal. The authors focused on two metastable β titanium alloys: Ti-20Nb-10Zr alloy (TNZ) and Ti-20Nb10Zr-0.1Y alloy (TNZY), which were correspondingly blended from the starting powders shown in Table 1. Injection moulded green parts were dog-bone shaped with a length of 90 mm for tensile testing and rectangular shaped (50 x 6.3 x 3.4 mm) for fatigue testing.
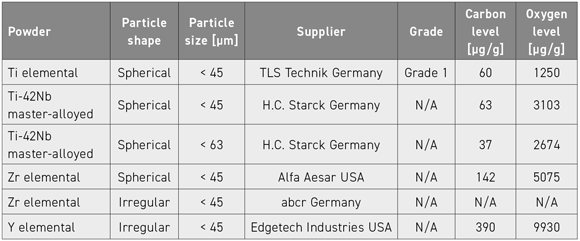
The moulded green parts were first immersed in n-hexane at 40°C for 15 h for debinding, and the (brown) parts were subsequently placed in a vacuum furnace for conventional thermal debinding (argon flow under 600°C at a constant gas pressure). This was followed by high vacuum sintering (at ca. 10−5 mbar and 1400−1500°C for 4 h with a set cooling rate of 10°C min−1). The authors stated that the oxygen levels of some as-sintered parts were roughly adjusted by a special heat treatment in mixed argon-oxygen gas at 500°C for different dwell times before final sintering after the pre-sintering stage (700°C/1 h). The carbon levels of some as-sintered parts were increased significantly to generate high carbon contamination by using a comparably ‘dirty’ retort without any burn-out clean-up programmes in advance. Finally, shot peening finishing was applied to the fatigue testing MIM parts to create compressive stress in an approximately 100−200 μm surface layer in order to erase surface defects such as open surface porosity.
The microstructures of the metastable β titanium TNZ and TNZY alloys were investigated, and the authors found a number of Y2O3 particles adjacent to porosity in the TNZY alloy (Fig.1(b)), and also that the coarse β grains contain differently oriented secondary α platelets as shown in Fig. 1(c). Residual porosity in the as-sintered β titanium alloy samples was found to be much higher (approx. 3-6%) compared to the porosity of as-sintered Ti6Al4V (2–3%). The porosity distribution of the investigated metastable β TNZ and TNZY alloys can also be seen in Fig. 1.
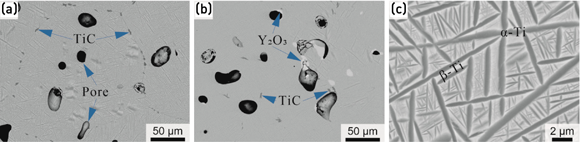
The authors stated that oxygen and carbon are the interstitial impurities which significantly influence the mechanical properties of MIM titanium alloys. They further stated that the current consensus is that the impurity contamination is mainly generated during the sintering process, partially from starting materials, and also from debinding processes. They reported that oxygen atoms in the interstitial solid solution state are able to affect the fracture mechanisms of (β) titanium alloys. However, for carbon atoms, once their content exceeds 60−230 μg/g (carbon solubility in β titanium alloys), carbon-deficient titanium-carbide (TiCx) precipitates. They are often located along prior β grain boundaries (GB) and seriously deteriorate the crack resistance (or damage tolerance) of β titanium alloys. The impurity levels and carbide fractions of investigated β TNZ and TNZY alloys produced in this research by using different processing parameters are listed in Table 2.
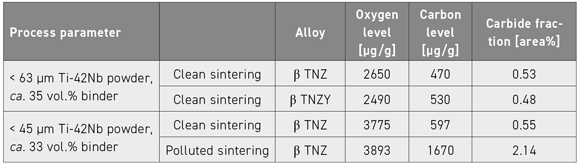
The authors investigated how the sintering temperature affected damage tolerance (i.e. a combination of strength and elongation to fracture) under static loading, and they also elaborated on the effects of oxygen solutes, carbide precipitates and secondary α precipitate (αs) coarsening behaviour on crack resistance of MIM β titanium alloys. The tensile properties of sintered β TNZ alloys with varying oxygen contents obtained by independent oxidisation treatments are shown in Fig. 2. The authors stated that it seemed plausible to increase the oxygen limit of metastable β titanium TNZ to around 3800−4000 μg/g, in order to obtain a favourable combination of strength and ductility.
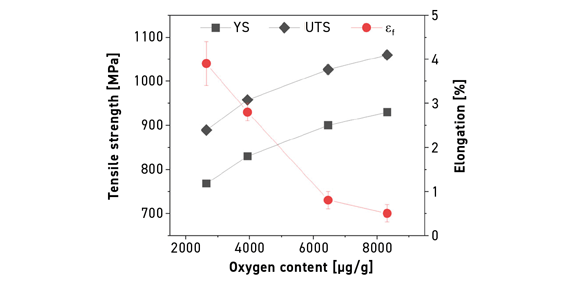
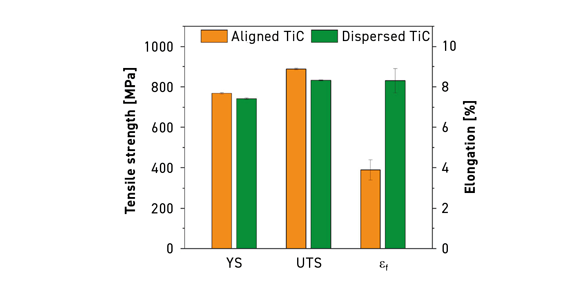
Fig. 3 shows the results of tensile testing of MIM metastable β titanium TNZ(Y) with either aligned GB-TiC or dispersed intragranular TiC precipitates, which are produced by a novel TiC redistribution method (CSRA sintering pathway) which the authors outlined in a previous paper. This involves a dissolution and re-precipitation heat treatment, where the grain boundary TiC (GB-TiC) precipitated at high temperature and high diffusion rate and is transformed into intragranular TiC precipitated at low temperature and low diffusion rate in large quantities, thereby adjusting the spatial distribution of TiC particles from alignment along grain boundaries to dispersion within grains. The authors state that, by regulating the sintering temperature in the β phase-field mass, diffusion rates can be increased or decreased. In this way, it is possible to change the residual porosity and prior β grain size in sintered β titanium TNZY alloys.
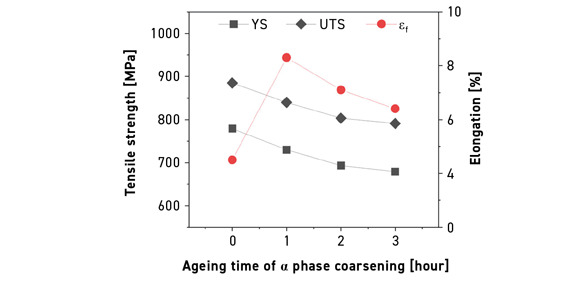
Fig. 4 shows the tensile properties of as-sintered β TNZY alloys which were heat treated at 800°C for 1 hour just below α/β transus for different holding times in order to coarsen secondary α precipitates. This precipitate coarsening treatment was found to result in a significant improvement in elongation.
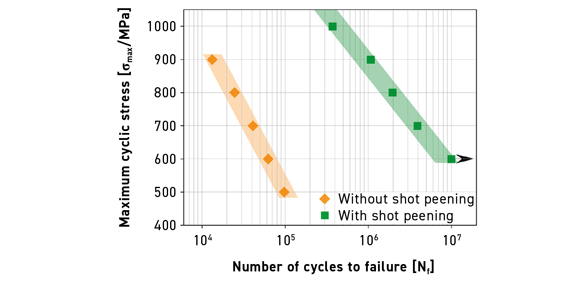
The authors also examined some defect-related factors that may affect the fatigue performance of sintered metastable β titanium alloys processed by MIM with surface quality being one of the most critical factors. Tests showed that shot peening enhanced the endurance limit (i.e. fatigue strength at 107 cycles) of MIM β TNZ alloys, and the results are shown in Fig. 5. It is clear that the fatigue life of samples without shot peening was less than one percent of that of the shot-peened ones. The authors noted that MIM metastable β TNZ provides superior fatigue performance, even ca. 150 MPa higher than MIM Ti6Al4V prepared by the prealloyed method. There is however, so far, no other data available in the literature to compare the fatigue properties of β titanium alloys processed by other PM routes.