Overview of producing highly porous titanium using the MIM/Space Holder process
September 24, 2022
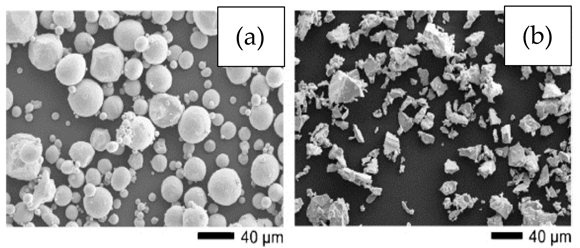
In a comprehensive review by a group of researchers at Federal University of Santa Catarina (UFSC), Brazil; the Universidad Técnica Federico Santa María, Chile. and the Santa Cruz State University (UESC), Brazil, recent advances in the processing of titanium via Metal Injection Moulding combined with the space holder method are presented. This manufacturing approach can be used to obtain porous medical implants which have high biocompatibility with the human body at the microstructural, chemical, and mechanical level. The twenty-one page review with ninety-nine references was published online in the journal Metals on April 30, 2022, with the lead author being Francisco Cavilha Neto at UFSC.
The review first focuses on the significant growth in the global demand for biomaterials which have emerged over the past two decades, and which provide excellent biocompatibility when used as biomimetic implants. The authors state that, in addition to good biocompatibility, biomaterials must also meet the following requirements: suitable mechanical properties (modulus of elasticity, yield strength, fatigue strength, wear and corrosion resistance) and a certain level of porosity to allow for osseointegration of bone into the implant. By definition, biocompatibility is a material’s ability to perform as a good ‘guest’ in a given application environment that requires interaction. The biological response is the local and systemic response of the host organism to the implanted biomaterial.
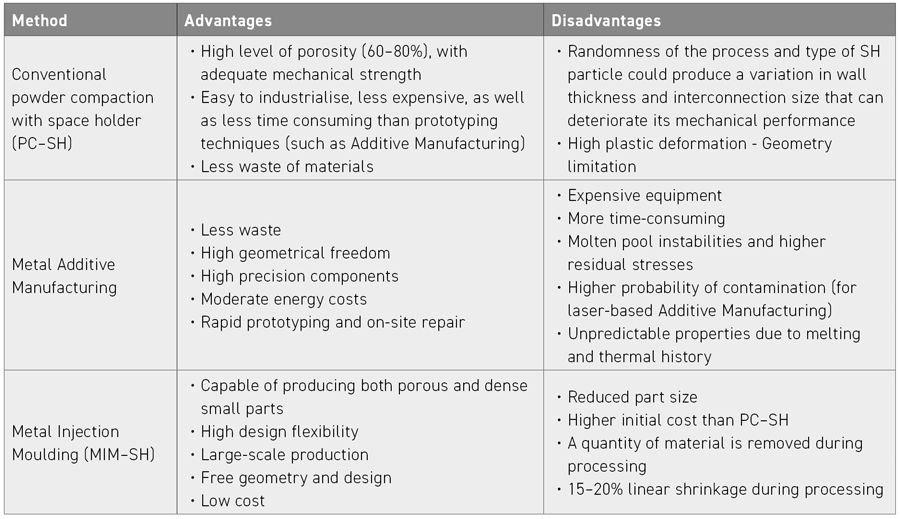
One of the main difficulties in achieving a very high degree of osseointegration is related to the difference between the elastic modulus of the implant material and the underlying bone structure. This can be overcome by the use of porous components manufactured using processes such as Metal Injection Moulding combined with the space holder (SH) method, powder compaction, and Additive Manufacturing (see Table 1). The pores generated from these processing methods, in addition to reducing the elastic modulus of the implant, provide the adherent surface necessary for cell proliferation and adhesion, thus avoiding the stress shielding effect. Furthermore, bone growth into the implant is determined by the porosity, pore size, and structure, allowing adequate vascularisation of cells and fluids. Good control over the required level of porosity must, therefore, be performed in order to achieve a precise balance between the mechanical properties and the biological and adhesion performance of the implant.
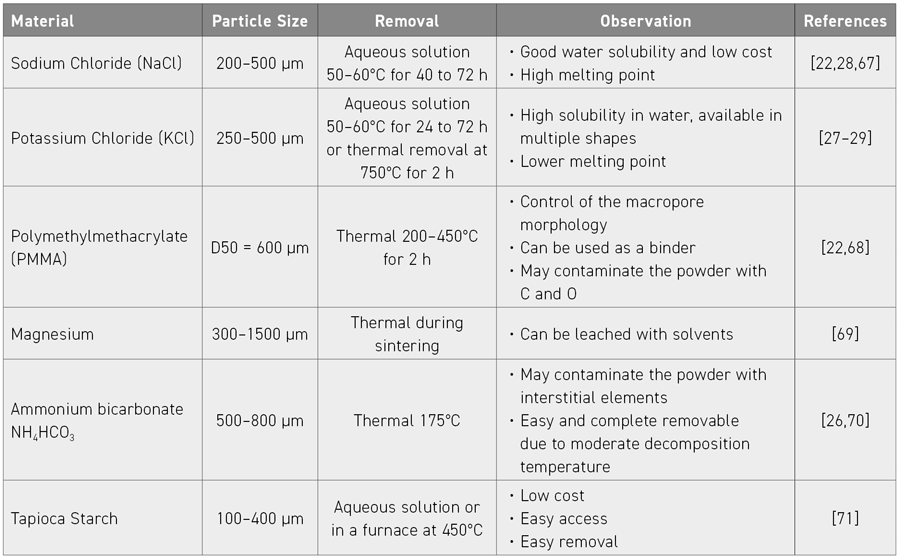
Several researchers are already reported to have applied the combination of MIM and SH to produce titanium foams with elastic modulus values close to those of bone, and pore percentages in the range of 30% to 72%. In this context, the authors of this review focus on the published advances made in processing foams using MIM combined with the space holder method for producing highly porous Ti implants. The suitability of different types of Ti powders, typical space holder materials (Table 2), plus processing parameters for feedstock preparation, injection moulding, binders and debinding and the removal of the space holder material, and, finally, sintering, are discussed in detail based on the authors’ experience to overcome problems that may affect the integrity of the final component, for example, those related to porosity, contamination, dimensional accuracy, and mechanical properties. Table 3 gives a summary of MIM/SH feedstock configurations found in the literature including some process and property data.
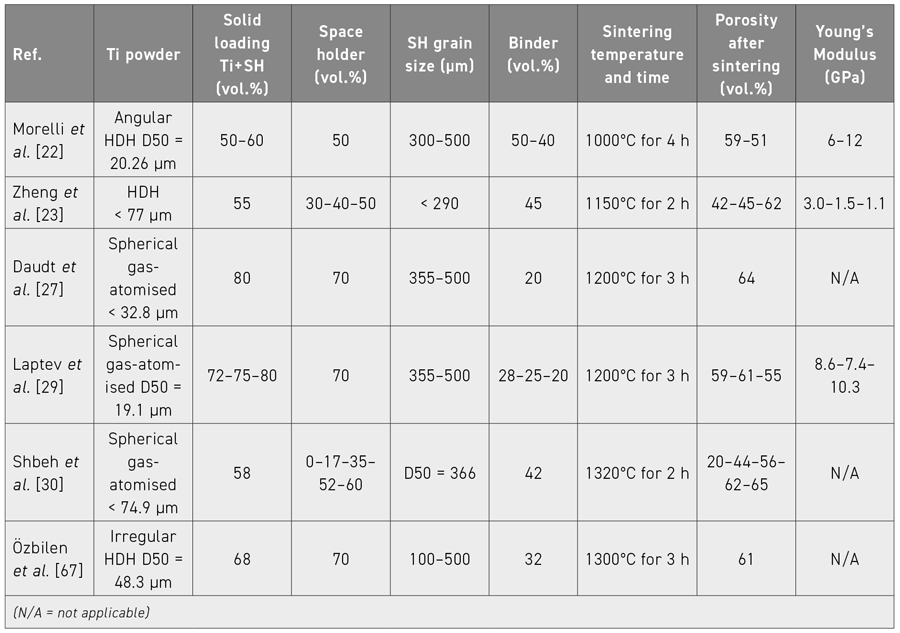
The authors stated that whilst there is currently still no commercial production of porous Ti implants for medical applications using MIM technology combined with the space holder method, they hope that their comprehensive overview will increase awareness regarding this promising technology among both researchers and MIM manufacturers. They highlight some of the new patents aimed at optimising the MIM route for producing porous Ti-based biomaterials, and conclude that to achieve the potential for this promising manufacturing route, the high cost of the initial Ti powder – which, ideally, should be a very fine powder with spherical particles – must be addressed. In this regard, studies underway on the use of low-cost HDH and TiH2 powders are promising, aimed at reducing the processing costs.
The problems concerning Ti powder shape and contamination are also under investigation to enhance the potential for the use of these powders by applying a protective atmosphere and/or plasma treatment. In addition, research on the control of process-induced contamination is being undertaken in terms of exploring, for instance, the use of hydrogen in the sintering process to reduce the oxygen content in the final porous sintered body. Finally, studies to address the problem of dimensional stability are being conducted. Plasma sintering may provide an important tool for achieving dimensional stability and, at the same time, assist in the removal of binders under a controlled atmosphere.