Linde to launch lab for advanced metal powders research
March 21, 2022
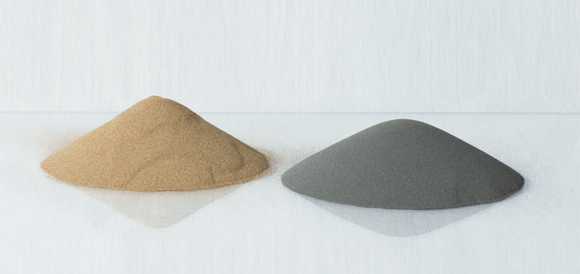
Linde, a global industrial gas specialist headquartered in Guildford, Surrey, UK, has announced that it will be developing a new, dedicated laboratory to advance the understanding of the parameters and behaviour of atmospheric gases used in the manufacture of metal powders. The new laboratory is due to become operational in mid-2022.
Linde explains that standard metal powder atomisers are unsuitable for the observation and analysis of gas behaviour as parameters are adapted. The focal point of Linde’s new laboratory, therefore, will be a much smaller-scale atomiser (1.6 m high) with specially adapted windows, lighting, high-speed cameras and schlieren imaging (a visual process used to photograph the flow of fluids of varying density), allowing for surveillance and data capture of each change of gas parameter. It will not rely on the introduction of molten metal, but use data from the simulated process to provide evidence of gas behaviour under certain conditions. The different parameters to be assessed include gas type, volume of gas, pressure and temperature, with the small atomiser able to rapidly switch over to analyse hundreds of combinations within minutes.
The laboratory is anticipated to enable Linde to develop new technologies to improve the atomisation process – particularly with regard to increasing yield and process stability. Linde will also collaborate with powder manufacturers and OEMs to help them test specific gas behaviours on the test bench, allowing them to then scale up the results on the companies’ own large atomisers.
“As demand grows for new metal powders, more research into the parameters of the gases which are integral to their manufacture is needed to ensure their role is optimised,” stated Pierre Forêt, Associate Director Additive Manufacturing, Linde. “Linde’s new laboratory will be the only one of its kind and is testament to Linde’s status as the leading authority on gases for Additive Manufacturing.”
For the atomisation of metals to create powders for Additive Manufacturing, a key challenge is maintaining a large volume of gas (2,000 m3/hour) under high pressure (60 bar or higher) and temperature (up to 400⁰C), even for a short period of time. When adding in factors such as metal type and gas composition, the variable parameters are immense and to analyse them requires not only the most advanced equipment, but reliable gas supply and experience.
A further key variable is the nozzle design which is responsible for injecting the specific gas, or gas mixture, at the required pressure and temperature. Linde will be able to offer powder manufacturers testing services to ensure optimal nozzle designs by additively manufacturing prototypes and testing them in the new lab.
While some academic institutions can undertake research into gas behaviour for the manufacturing of metal powders, Linde states that it is the only organisation with the capacity to draw on a readily available supply of gases.