Foerster offers new induction thermography part testing
January 12, 2022
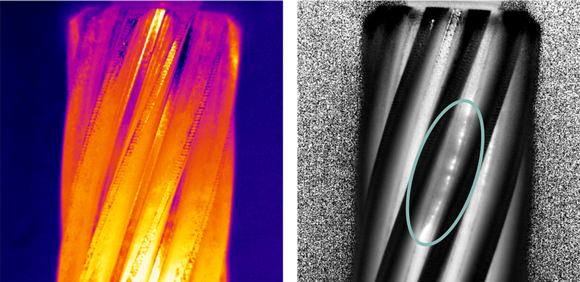
Foerster Group, headquartered in Reutlingen, Germany, has introduced a new, non-destructive automatable solution for testing sintered components using induction thermography. The technique allows for contact-free crack detection on metal components, and is particularly suited to parts with complicated shapes where test areas can be difficult or impossible to access with eddy current probes.
The process is reported to identify open cracks, pores, heat treatment cracks, forging laps, welding defects, etc. It can be used on rough, uneven surfaces and surfaces coated with water or oil, with testing done in less than one second.
The induction thermography method is suitable for the examination of semi-finished products as well as complexly shaped components. A current induced into the workpiece generates localised hotspots at the defects in the material. These hotspots can be detected through their heat radiation with an infrared camera.
A typical system consists of an infrared camera and an inductor, with a generator for high-power pulses. The inductor is positioned such that a magnetic field pulse induces currents in the test area, heating the part by a few degrees Celsius. Simultaneously the camera is recording the area. The camera captures the heat radiation, which is emitted as infrared light, and creates a temperature image of the surface.
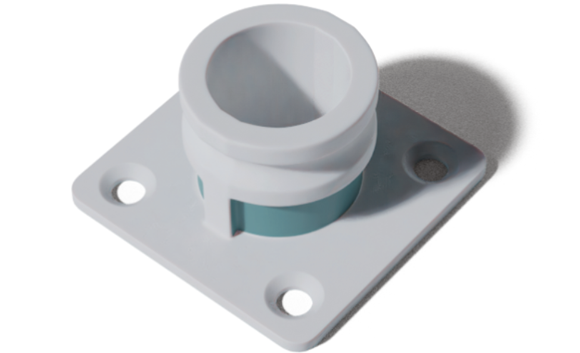
If there are defects (cracks) in the test area, the induced current is deviated and is locally displaced or squeezed. Consequently, those locations in the part are heated stronger. When such hotspots form directly at the surface, they emit heat radiation and are visible to the camera. The heat from hotspots within the material can also reach the surface through the heat conduction of the material. However, the range into the material is limited by the penetration depth of the induction.
The thermal recordings are analysed with video and image processing algorithms. On a thermography recording, the hotspots leave a crack signature similar to a string of pearls. In contrast, other surface features, such as roughness and scratches, are suppressed. This way cracks can be detected that would be difficult or impossible to distinguish in a conventional photo. The high contrast and characteristic shape of cracks in induction thermography images allows for reliable algorithmic detection and enables the full automation of the procedure.
Induction thermography is said to offer a particular advantage on components that have special structural properties, such as threading, gearing, blades or profiles. Suitable parts include those that are forged, sintered and additively manufactured.