ExOne qualifies Inconel 718 for binder jet AM applications
August 5, 2020
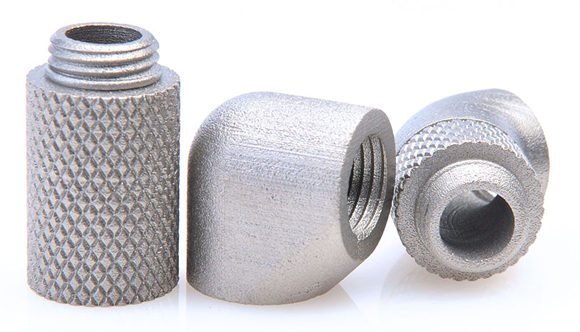
The ExOne Company, North Huntingdon, Pennsylvania, USA, reports that the nickel-base alloy Inconel 718 has been certified as Third-Party Qualified, the company’s highest designation of material readiness for its binder jet metal Additive Manufacturing machines.
Frequently used in the aerospace, energy and automotive industries, Inconel 718 is known for its high strength and hardness, with strong resistance to corrosion, chemicals and extreme temperatures ranging from sub-zero to 704℃. It also has outstanding welding characteristics and is often used for high-temperature applications such as jet engines and tooling, or corrosive environments, such as those featuring seawater or acids.
“Today’s qualification of Inconel 718, following on the heels of M2 Tool Steel earlier this year, shows the ExOne R&D team is aggressively delivering new materials for binder jet 3D printing,” stated Rick Lucas, ExOne CTO and VP, New Markets. “Our increasing pace of material qualifications is a testament to the strength of our new metal 3D printer systems equipped with Triple ACT, an advanced compaction technology that is essential for Binder Jetting metals and other materials at high speeds and densities.”
The company explains that as is the case with Inconel 718, ExOne’s patented Triple ACT enables the Additive Manufacturing of standard MIM powders, followed by the use of standard sintering profiles and heat treatments, that deliver high-density results consistent with wrought material. Independent testing verifies that Inconel 718 additively manufactured and sintered by ExOne meets ASTM standard B637-18.
Lucas added, “ExOne can now transition R&D materials to full qualification as demand increases.” ExOne has three tiers of material qualification, used to signify the varying levels of readiness of materials for binder jet AM applications: R&D, Customer-Qualified and Third-Party Qualified.
Previously, the company had recognised Inconel 718 as an R&D material, which meant it had been deemed buildable for researchers, supported by ongoing development. The new Third-Party Qualified status means that the material has passed rigorous ExOne tests over multiple builds and has verified material property data from an independent third party.
Customer-Qualified materials are those that have been qualified by ExOne customers with their own standards and are currently being successfully additively manufactured for their own applications. However, they have not yet earned ExOne’s highest level of qualification for general market readiness.
Currently, twenty-two metal, ceramic and composite materials are Third-Party or Customer-Qualified. In addition, more than two-dozen materials are recognised as R&D ready, including aluminium, which has been fast-tracked for qualification. ExOne believes the ability to additively manufacture aluminium at high speeds will have a transformative, sustainable effect on the automobile and aerospace industry.
The company explains that its proprietary CleanFuse binder was a critical component in the new qualification of Inconel 718. CleanFuse is a clean-burning binder for additively manufactured metals that are sensitive to carbon left behind by other binding agents during sintering.