Defining when filament-based MEX could replace Metal Injection Moulding
February 3, 2023
Fig. 1 The three stages of MEX and MIM processing (From paper: ‘Additive manufacturing of metal filament: when it can replace metal injection moulding’ by A Quarto and C Giardini, published in Progress in Additive Manufacturing, 21 September 2022, 10pp.)
In recent years, there have been a number of advances in metal Additive Manufacturing technologies, making them attractive alternatives to both subtractive manufacturing processes as well as net- or near-net shape processes such as Powder Metallurgy and Metal Injection Moulding. This is particularly the case for metal components with higher levels of complexity, which would benefit from weight saving possibilities and require a relatively low volume of parts. It is well known that MIM is capable of producing highly complex shapes and at required production volumes using a wide range of metals and alloys to achieve the desired part performance and cost. However, MIM is considered relatively expensive in terms of energy and investment in production equipment and tooling. Competing with MIM are a number of metal AM processes, but many of these, such as Laser Beam Powder Bed Fusion (PBF-LB) are also high energy users with often lengthy production times and are not thought to be suitable for low-value parts or for high part volumes.
One metal AM process attracting the attention of producers is material extrusion (MEX), the ISO/ASTM term for the process referred to as Metal-ME in the reviewed paper, because of its flexibility and potential for producing complex shapes with lower investment costs compared with MIM. MEX has recently been adapted for extruding metal filaments – for example, AISI 316L and 17-4 PH, with feedstock for the filaments comprising 80 wt.% stainless steel with a 20 wt.% polymer content, which allows easy printing. MEX also shares a common stage of the production chain with MIM – namely, debinding and sintering. The two processes are said to have the ability to produce complex geometries, high-density parts (98.7% for MEX and 99.2% for MIM) and the possibility to use several different metals and alloy materials.
In order to gain more information on which of the two processes has the best commercial potential, University of Bergamo, Dalmine, Italy, has carried out a study which aimed to develop a cost model for a selected part produced by MEX and MIM. The model included the evaluation of the MEX and the MIM processes production cost trends, investigating how these processes can be characterised by different behaviour as a function of the production volume and the number of parts obtained within a single production cycle. The results of this study were included in the paper ‘Additive manufacturing of metal filament: when it can replace metal injection moulding’ published in Progress in Additive Manufacturing.
The authors of the study – Mariangela Quarto and Claudio Giardini – stated that, although MIM and MEX may both be successfully used to produce a specific part, it is the economic aspects, such as the expenditure of time, money, and resources (including energy) related to the whole production chain, which must be considered. The results of their study has, therefore, made it possible to develop a model for the study of the part unit cost, the productivity rate, and the dummy time (DT). Dummy time is said to represent how many hours are theoretically necessary for producing a single part.
The process chain for the two manufacturing processes is shown in Fig. 1 and involves three stages. The first stage mainly involves costs related to the time spent on the design of the product and/or of the mould (for MIM) and for defining the tool/nozzle path (for MEX). These costs are considered hidden ones (except for the mould used in MIM, which is included in the consumable costs). The second stage involves actual part production to the green part stage and the third stage is omitted in the cost model, because the same type of material is used and the same external company is performing the debinding and sintering and will, therefore, have the same cost.
It is evident from the first stage that the time interval from conceptualisation of the part to the start of production is significantly shorter for MEX taking 2-3 days to define the tool/nozzle path for Additive Manufacturing. For MIM, the process is longer, since the design, the optimisation (even through simulations) and the realisation of the mould are fundamental prerequisites. These activities could take between 10-15 woking days for not very complex parts, and could be longer if the complexity level of the components and, consequently, of the mould increase. The authors stated that the duration is strictly related to the requirements of the designed part.
The authors further stated that a key challenge in component design and production is weight reduction or improving the cooling of critical components. A number of researchers have used turbine blades as an example, by generating a hollow structure for weight reduction and external micro-holes for improving cooling. Both MEX and MIM are considered suitable technologies for turbine blade production. However, only MEX allows hollow turbine blade parts to be produced in a single process, whereas similar hollow features could not be realised by the MIM process and the micro-holes for improving the cooling of the parts would require additional micro-EDM machining.
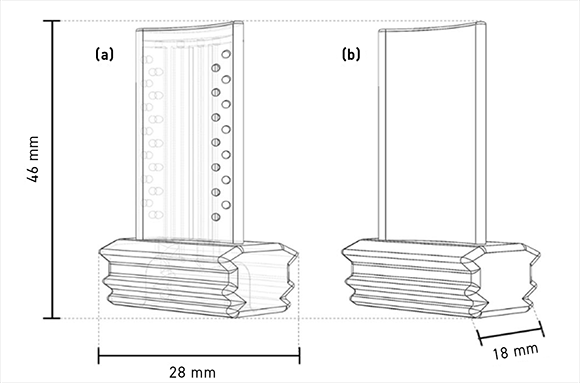
The design of the 316L stainless steel turbine blade used in this study is shown in Fig. 2. The turbine blade produced with cooling holes and internal hollow structure using MEX shown in Fig. 2 (a)) resulted in a mass/volume reduction of 24%. The authors stated that it would be impossible to produce the same internal hollow features and the cooling holes in the MIM turbine blade without additional machining processes.
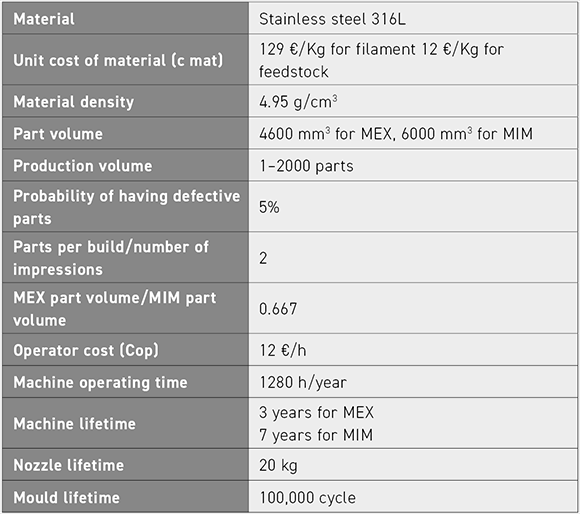
Table 1 shows the main data inserted into the cost model. As can be seen in Fig. 3 for both MEX and MIM, the increment in Nord (defined as the size of the customer order) causes a reduction in the unit cost (UC), generating a monotonous decreasing curve. For MEX, it is evident how the first part of the curve is characterised by a rapid decrease of the cost as the production volume increases, presenting an almost horizontal asymptotic trend (i.e., the cost becomes approximately constant). The situation is different for the MIM process, which is characterised by a more slowly decreasing trend. In the zoomed area, shown in Fig. 3(a), the inversion of the economic convenience for the two technologies is evident.
Fig. 3 Unit cost (UC) – (a) productivity rate (PR) – (b) and dummy production time (DT) – (c) for the MEX and the MIM process varying the production volume
A second analysis of the costs looked at the number of parts produced in a single working cycle. In MEX Additive Manufacturing, more than one part on the same plate will reduce the total time due to the set-ups, while the cost will remain constant. For MIM, increasing the number of mould cavities does not necessarily reduce production costs, but will considerably reduce production times. However, MIM turbine blades will require further micro-EDM machining of the external cooling holes and the MIM parts cannot be produced hollow to achieve weight savings. The result is that, with the need to use the micro-EDM machining process for the cooling holes, the cost curve for MIM moves upward and the authors were able to draw a window defining the maximum and minimum costs of the combined process. At this point, it became evident from the cost study data that MEX becomes the less expensive solution, regardless of the production volume.
www.springer.com/journal/40964
Download PIM International magazine
