CIM provides added value for controllable automotive water pumps
February 1, 2019
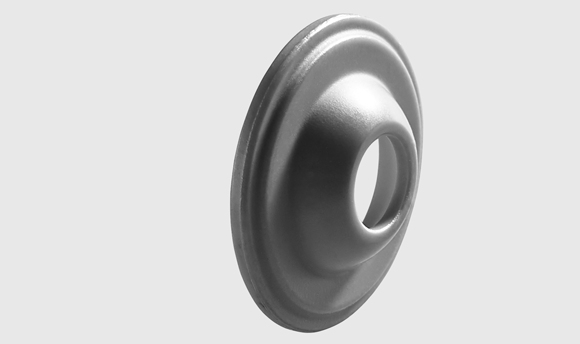
The new sliding shoes are manufactured in Si3N4 using CIM (Courtesy Arburg)
FCT Ingenieurkeramik GmbH (FCTI), Frankenblick, Germany, has replaced a Diamond Like Carbon (DLC) coated steel sliding shoe, used in controllable automotive water pumps, with a new sliding shoe produced from high-performance silicon nitride (Si3N4) manufactured by Ceramic Injection Moulding.
Sliding shoes made from Si3N4 offer a major advantage in controllable water pumps in that the material enables optimised friction. In motor vehicles, this results in both reduced power consumption and reduced CO2 emissions.
The task of the sliding shoes is to convert rotary motion into a linear piston movement in an axial piston pump, while simultaneously serving as an active thermal management component for media routing. For this reason, the parts must have high resistance against water, acids, fuels and anti-freezes, must be low weight, and must have high temperature resistance and high dimensional stability, as well as be produced using a reliable and stable manufacturing process. A high level of traceability, quality and flexibility must also be ensured during high-volume production of the sliding shoes, which are used in controllable water pumps for the Volkswagen Group.
In developing the CIM sliding shoes, the partnership between the part developer and customer, Nidec GPM GmbH (NGPM), Auengrund, Germany, and the manufacturer, FCTI, extended to the production of prototype parts, various bench tests and the construction of a first trial mould featuring near-production shapes. This was followed by a further testing programme lasting several months in order to ensure the parts complied with all relevant standards and requirements.
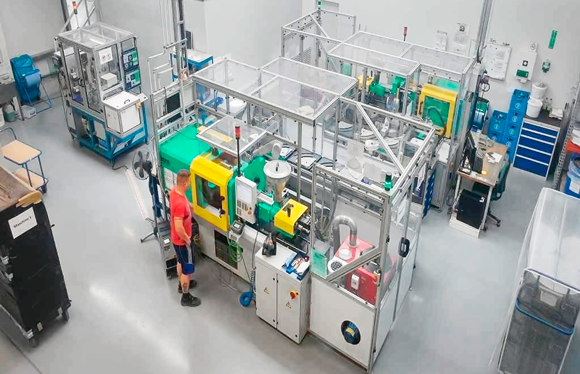
The sliding shoes are produced on Arburg AllRounders equipped for CIM (Courtesy FCT Ingenieurkeramik GmbH)
Frank Stegner, Project Manager Automotive at FCTI, stated, “From feedstock development and production, which were carried out using eMBe Products & Service GmbH in Thierhaupten, through to injection moulding, the sintering process and final lapping, we were able to cover the complete manufacturing and machining operation. Arburg then came into play with its injection moulding technology. Ultimately, we obtained the contract largely as a result of this knowledge.”
Since September 2017, FCTI has been injection moulding the ceramic sliding blocks on two hydraulic Arburg AllRounder 270 S machines with 4-cavity moulds. On both machines, part removal and set-down in trays is performed by a six-axis robot. Green compacts shrink by approximately 20% during sintering, which is followed by grinding, lapping and polishing.
Stegner commented that he is highly satisfied with the cooperation between FCTI and Arburg. “We already received excellent advice in the run-up to the machine purchase – from extensive preliminary tests through to customised compound development. Arburg’s extensive experience in the field of CIM helped us a great deal.”
“The use of the ceramic material has led to reduced friction losses,” he added. “This means that both the power consumption and the CO2 emissions can be sustainably reduced. The power consumption of each water pump has been reduced by approximately two watts. Over two million pumps, this represents an annual saving of some 4,000 kilowatts. Extrapolated to an average annual mileage of 14,000 kilometres per car at an assumed average speed of 50 kilometres per hour and an average driving time of 282 hours, this results in a CO2 saving of about 983 tonnes.”
www.arburg.de
www.fcti.de
www.embe-products.com
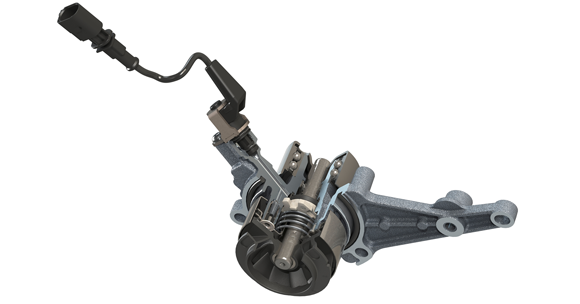
The sliding shoes are used in automotive water pumps (Courtesy FCT Ingenieurkeramik GmbH)