China’s specialist MIM powder producers expand production to meet growth
November 20, 2018
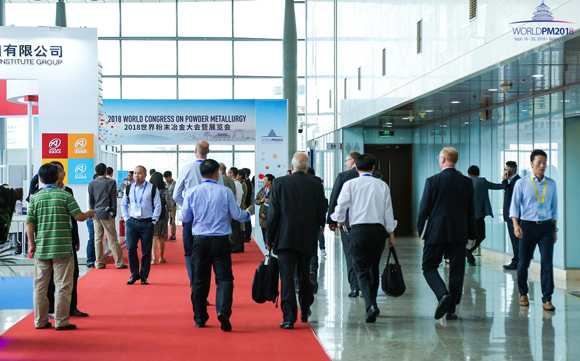
The 2018 World Congress on Powder Metallurgy took place in Beijing, China, September 16-20, 2018 (Courtesy World PM2018)
The 2018 World Congress on Powder Metallurgy (World PM2018), held in Beijing, China, September 16-20, 2018, highlighted the high rate of growth that has been achieved globally in Metal Injection Moulding (MIM) part production over the past decade, and more specifically the contributions made by China’s MIM producers and powder suppliers to this growth. This contribution was very evident in the number of specialist Chinese powder producers, some of which are relatively new to the field, which exhibited at World PM2018 .
Speaking to Bernard Williams on behalf of PIM International, most of those specialist powder companies who exhibited at the world congress stated that they were in the process of increasing production capacity for fine spherical powders in order to meet the continuing growth in demand from both the MIM and metal AM sectors. A number of companies reported that they are using advanced processes such as combined high pressure water and gas atomisation to produce the MIM grade powders.
Tianjin Zhujin Technology Development Ltd was established in 1990 in Beichin, Tianjin, to produce a range of Fe-, Ni- and Co-based alloy powders for thermal spraying, hardfacing, and other applications.
Since then, the company has further refined its gas atomisation technology to develop alloy powders for Powder Metallurgy, Metal Injection Moulding and metal Additive Manufacturing for high-performance applications, including a complete range of stainless steel powders having fine particle size, low O2 content and high sphericity. The most recent expansion in powder production facilities is reported to have taken the company’s annual capacity to around 30,000 tonnes.
Advanced Technology (Bazhou) Special Powder Ltd is a company established in Bazhou City, Hebei Province, as a joint venture between AT&M and Hebei Hengxin Trading Ltd in October 2017. Powder production lines using gas and water atomisation were transferred from AT&M in Beijing to Bazhou, and with the additional new atomisation lines the company will have annual capacity of 10,000 tonnes – making it one of the largest specialist powder manufacturers in China. Powders are produced for MIM, soft magnets, diamond tools, automotive parts and filters.
Yingtan Longding New Materials & Technologies Ltd was established in the Haidian District of Beijing as recently as 2011 to produce atomised powder for MIM using advanced gas and water atomisation, as well as a combined gas and water atomising process. The company reported sales of 2,700 tonnes in 2017 and is expanding production with a new powder plant that will go on stream in 2019, having a capacity of 5,000 tonnes/year.
Changsha Hualiu Metal Powders Ltd (HL Powder), based in Changsa, Hunan Province, currently operates six gas atomisers having annual capacity of around 3,600 tonnes for stainless steel, soft magnetic and other special alloy powders. The powders are produced primarily for use in MIM, metal Additive Manufacturing, powder cores, etc.
Jiangxi Yuean Superfine Metal Ltd (formerly known as Yuelong Powders) is located in the Jiangxi Province, and is one of Asia’s leading producers of carbonyl iron powders (CIP). The company has established a leading position in China as a supplier of MIM feedstock using its CIP powders and, in 2010, added water and gas atomisers for the production of high quality stainless steels, iron-based alloys, Ti and Ti alloy powders for use in MIM as well as Additive Manufacturing.
Huijing Atomizing Science Ltd, based in Deqing, Huzhou Province, has been manufacturing a range of metal and alloy powders for MIM since 2000. The company introduced high-pressure water atomisation technology to produce fine, spherical stainless steel powders in 2006 (having D50 particle size of 7.5 µm). The 316L stainless powder is said to have an oxygen content of around 2500 ppm, and can be sintered 7.85 g/cm3 density. In 2015, it began production of Ti alloy powders.
Lide Powder Material Ltd, based in Shijiazhuang, Hebei Province, has been producing MIM grade powders (mainly stainless steels) for around ten years and now has six production lines using its super-high pressure water-gas atomisation technology, giving an annual capacity of 4,600 tonnes of metal and alloy powders. The company states that its F75 grade Co-Cr atomised powder is used to produce the MIM camera frame used in the casing of Apple’s iPhone X.
VTECH, part of Vday Additive Manufacturing Technology Ltd, based in Changsha, Hunan Province, produces a range of micro and nano powders from Ti alloys, Ni-based superalloys, stainless steel and high alloy steels, suitable for both MIM and metal AM. It also produces a range of amorphous alloy powders.
CNPC Powders recently completed the construction of a new 30, 000 m2 facility in Fengyang, Anhui, that will have an annual production capacity of 3,500 tonnes of metal powders for AM, MIM and other applications. The powders produced will include iron and copper alloys, Ni-base alloy, Ti alloys, stainless steels, Co-based alloys and electrolytic copper and chromium powders.
DAYE Metal Powder Ltd (DY Powder) has been based in Yuanshi County, Shijiazhuang Province, since 1998, producing MIM and AM grade stainless steel powders by a combination of ultra-high pressure water and gas atomisation. The fine, nearly spherical atomised particles have a smooth surface and an O2 content of 2200 ppm at D50 of 12 µm.